全球灯塔工厂是由世界经济论坛与麦肯锡公司于2018年共同提出,审查方式是由独立的专家小组,评选出运用人工智慧(AI)、工业物联网(IIoT)、大数据等技术提升效能与获利的指标型工厂,评比范围涵盖30个国家和35个不同的产业,目前全球累积已有189座灯塔工厂。
联电于2017年成立专责推动数位转型的「智慧制造处」,率先以南科作为主要先导示范厂区,并逐步推展至其他生产据点。智慧制造处成立至今,透过将工业4.0技术整合到营运及上下游价值链,成功累积超过48件解决方案,其中近95%由联电自主研发。透过这些解决方案,Fab 12A厂成功缩短57%的设计套件交付时程,提升产品良率至97%,同时增加47%的工作效率,进而提高客户黏著度、整体制造效能与产品品质,对企业的营运及获利做出贡献。
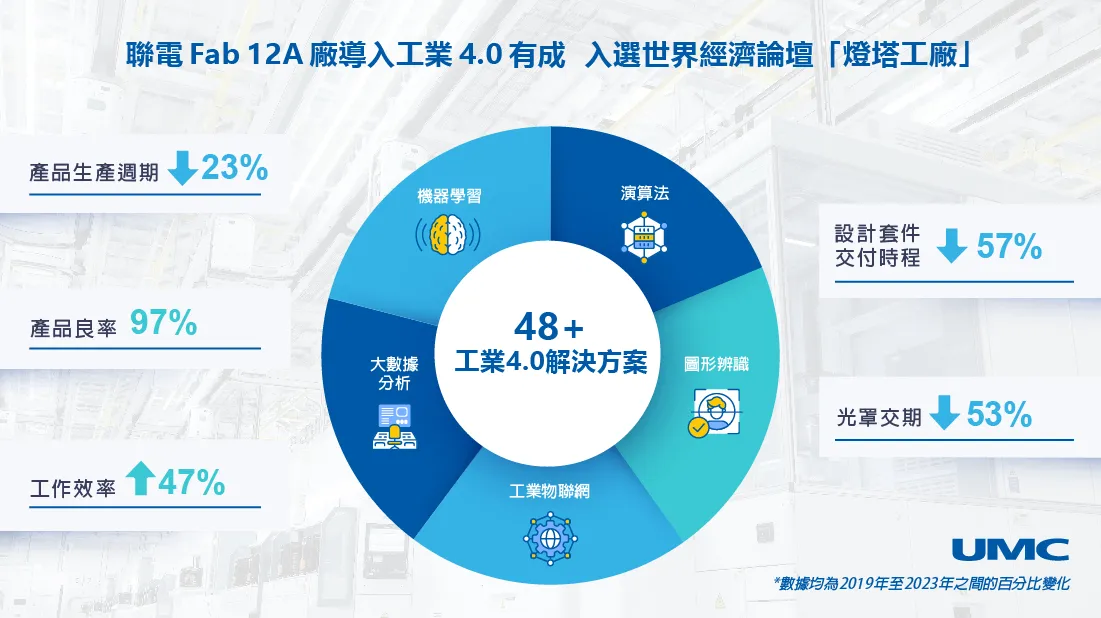
联电副总经理吴宗贤表示:「我们很荣幸能够获得世界经济论坛的认可,成为以大规模运用尖端技术于制造业的数位转型先驱。联电以工业4.0为永续发展的核心,确保我们在日益竞争的市场中满足客户需求。智慧制造不仅可提升员工能力和工作效率,让同仁专注于更有价值的工作,更在生产过程中优化各项资源使用上,降低对环境的冲击。身为引领产业数位转型标竿,联电也将持续向其他在灯塔工厂网络中的企业学习。」
联电致力提供高价值的晶圆特殊制程解决方案,然而由于特殊制程对于规格的要求更趋于严格及精确,其复杂度也随之提升。在工业4.0技术的助力之下,可有效应对特殊制程的复杂度及严苛标准,进而提升客户的黏著度,让联电在激烈竞争的市场中脱颖而出,进一步提升企业的整体获利能力。
联电运用核心技术的导入和开发应用,推展出多方面的智慧制造专案。其中为了加速客户产品的上市时程,运用机器学习工具,缩短设计套件交付时程一半以上。再来,为确保光罩的准确性和交付时间即时性,联电开发了人工智慧平台,借以精简公司和客户及供应商之间的资料处理流程。
此外,为了缩短产品生产周期,联电针对制造过程中的瓶颈机台,采用「机器学习模型预测」和「智慧气体切换系统」,缩短产品在生产过程中因气体切换的调机与等待时间;同时也建立「智慧缺陷真因辨识系统」,结合智慧影像识别和自动化AI智能异常搜查比对系统,帮助工程师在极短时间内找出真因和造成缺陷异常的机台,有效提升产品良率。
此次入选灯塔工厂的联电Fab 12A厂是由三个独立且相连的厂房组成,透过智慧自动物料传送系统(Automated Material Handling System; AMHS)串连3,000部机台和6,800万条可能的传送路径,将晶圆在跨厂区间进行自动化传送。联电整合AI演算法和AMHS系统,可自动为每片晶圆规划出最佳的传送路径,全面提升工作和晶圆传送的运输效率。
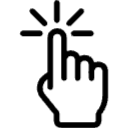